When I was eleven my parents took me to Disney World in Florida. I don’t remember much about the trip other than we rode space mountain, went to Epcot, and did the backlot tram tour at what was then called MGM Studios.
And I remember the burger I had one night at a restaurant on International Drive.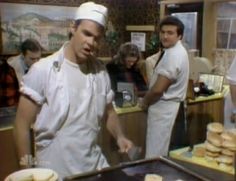
It was the juiciest, tastiest burger I had ever had.
It was really undercooked, I ordered it medium rare.
I don’t think ordering burgers undercooked was an option in Ontario. I had never been offered a choice before.
No one told me or my parents that there was increased risk of illness eating undercooked meat. Maybe there was a consumer advisory on the menu. But probably not, I don’t remember seeing it. This was 1989, before Jack-in-the-Box. After McDonalds in 1982.
While golfing at IAFP in 2005, Doug and I were in line for burgers in-between the front and back nine. The cook asked the group in front of us how they wanted their burgers. One guy responded, “Bloody … with cheese.”
No one said anything about the risks.
Over the next nine holes we talked about servers as risk communicators, figuring out what they knew, what they said and how to get better information to patrons.
Years later, as part of a USDA CAP grant my former PhD student and current Food Safety Scientist at RTI International, Ellen Thomas, would lead the first part of this work and found that servers aren’t great at helping folks makes informed decisions. That paper was publish today.
NC State University’s press release about the paper is below.
Front-line staff, such as servers in restaurants, are often trusted with providing customers with food safety information regarding their meals. A challenge to the industry is that these positions have high turnover, relatively low wages and servers are focused primarily on providing patrons with a positive experience. And new research shows that this poses a problem.
A recent study finds that restaurants don’t do an effective job of communicating with customers when it comes to addressing risks associated with eating undercooked meat – specifically hamburgers. Inaccurate information provided by servers often contradicts science-based information customers need to make informed food safety decisions.
All 50 states in the U.S. have adopted some version of the Food & Drug Administration’s Model Food Code, which requires restaurants to tell customers about risks associated with undercooked meat and poultry products. Such as hamburgers.
“We wanted to know how well restaurant servers and menus communicated with customers about these risks, specifically in the context of beef hamburgers,” says Ben Chapman, co-author of a study on the work and an associate professor at North Carolina State University whose research program is aimed at improving food safety.
The researchers focused on beef hamburgers because consuming undercooked ground beef has been linked to a lot of foodborne illness outbreaks, including outbreaks related primarily to Shiga toxin-producing E. coli.
For this study, the researchers sent trained “secret shoppers” into 265 full-service, sit-down restaurants in seven different regions around the U.S. At each restaurant, the patrons ordered one well-done hamburger and one medium-rare hamburger to go. The shoppers then recorded how, if at all, the restaurant communicated about risk.
This study is the latest in a long line of real-world research that Chapman and his collaborators have conducted.
“We try to actually match what people do versus what they say they do because people will say anything on a survey,” says Chapman “We’ve looked at cooking shows; observed handwashing and cross-contamination in commercial kitchens; hand hygiene during a norovirus outbreaks and others. What people actually do is the difference between an enjoyable meal and a foodborne illness.
“For example,” Chapman says, “did the server mention risks associated with undercooked meat when the shopper ordered? If not, the shopper would ask about the risk of getting sick, and then record whether the wait staff responded with clear, accurate information.”
The shoppers also looked to see whether restaurants included clear, accurate risk information on their menus.
The study found that 25 percent of restaurants wouldn’t even sell an undercooked hamburger to secret shoppers. However, at restaurants that would sell a medium-rare hamburger, the majority of servers – 77 percent – gave customers unreliable information about food safety.
“Servers said that meat was safe because it was cooked until ‘until the juices ran clear’ – which is totally unreliable,” says Ellen Thomas, a food safety scientist at RTI International and lead author of the study who worked on the project while a Ph.D. student at NC State. “Those 77 percent didn’t mention things like cooking meat to the appropriate temperature – either 155°F for 15 seconds, or 160°F for instant kill.
“The indicator of safety most widely-reported by servers was the color of the burger, and that’s also not a reliable indicator at all,” Thomas says “Time and temperature are all that matter. And undercooked, unsafe burger can be brown in the middle, and a safely cooked burger can still be red or pink in the center.”
Meanwhile, almost all of the menus complied with FDA guidance. But what servers told customers often contradicted the information on the menu.
“If a menu says something is risky but a server says that it isn’t, that can downplay the risks for consumers and impact a customer’s decisions,” Chapman says. “It’s confusing, leaving the patron to choose which message to believe”
The researchers also found that chain restaurants fared much better than independent restaurants at having servers offer reliable risk information.
“That’s not surprising,” Chapman says. “Large chains implement standardized training across all outlets for servers in order to protect their brand and reduce the likelihood of being implicated in a foodborne illness outbreak. That’s bad for business.
“This study tells us that servers aren’t good risk communicators,” Chapman says. “We encourage consumers to ask food safety questions, but they should probably ask a manager.
“It also tells us that we need to work on addressing the widespread – and wrong – belief that color is a reliable indicator of food safety in meat,” Chapman says. “Restaurants are in a position to help us share this information with consumers, but many servers are currently sharing incorrect information.”
The paper, “Assessment of Risk Communication about Undercooked Hamburgers by Restaurant Servers,” is published in the Journal of Food Protection. The paper was co-authored by Andrew Binder, Anne McLaughlin, Lee-Ann Jaykus, and Dana Hanson of NC State; and by Doug Powell of barfblog.com. The research was supported by Agriculture and Food Research Initiative Competitive Grant no. 2012-68003-30155 from the USDA National Institute of Food and Agriculture.
Abstract: According to the U.S. Food and Drug Administration 2013 Model Food Code, it is the duty of a food establishment to disclose and remind consumers of risk when ordering undercooked food such as ground beef. The purpose of this study was to explore actual risk communication activities of food establishment servers. Secret shoppers visited restaurants (n=265) in seven geographic locations across the U.S., ordered medium rare burgers, and collected and coded risk information from chain and independent restaurant menus and from server responses. The majority of servers reported an unreliable method of doneness (77%) or other incorrect information (66%) related to burger doneness and safety. These results indicate major gaps in server knowledge and risk communication, and the current risk communication language in the Model Food Code does not sufficiently fill these gaps. Furthermore, should servers even be acting as risk communicators? There are numerous challenges associated with this practice including high turnover rates, limited education, and the high stress environment based on pleasing a customer. If it is determined that servers should be risk communicators, food establishment staff should be adequately equipped with consumer advisory messages that are accurate, audience-appropriate, and delivered in a professional manner so as to help their customers make more informed food safety decisions.